Topic(s): Vacant Land Stewardship
Vacant industrial spaces are reborn to support a new age of small-scale manufacturing
December 17, 2015
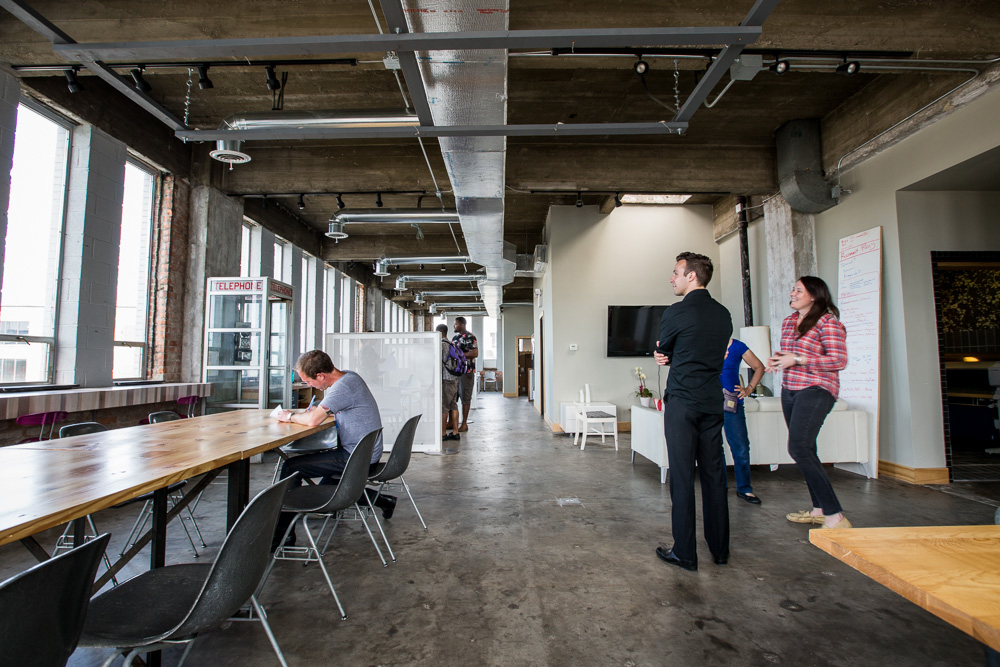

View of Downtown Detroit from Shared Working Space at Ponyride (Credit: Chris & Michelle Gerard)
There’s a myth surrounding post-industrial economies, Dan Kinkead, acting executive director of Detroit Future City, shares in conversation about the rebirth of small-scale manufacturing in his hometown of Detroit.
“The myth is that we need to build new economies around technology and innovation completely divorced from industry,” said Kinkead. “But industry is actually evolving and is now highly innovative today.” It’s just on a different scale.
Small outfits working on everything from 3D printing to furniture design are forming in cities like Detroit, and they are looking for space to work. Luckily, in most Legacy Cities, there is a surfeit of vacant industrial space that is proving ripe for rebirth as shared spaces for small-scale manufacturing, where entrepreneurs can rent space in common. Small-scale manufacturing is an umbrella term used for all small businesses producing tangible goods (You can find a full glossary of related terms here).
Dan describes it as “a circular moment where we’re reutilizing things that we already have. Cradle to cradle.” Many of the large-scale industries that once powered the rapid growth of Legacy City economies are now long gone. The entrepreneurial spirit that fueled that growth has not perished, though, and it is that ethos that is the driving force behind this new rise of manufacturing.
That alone, however, is not enough. In order to truly start a manufacturing renaissance in Detroit and in other cities like it, local governments need to think more about how to create policy and regulation that directly supports the reuse of vacant industrial space for small-scale manufacturing. They will also have to think about how best to help reuse projects secure the funds they need to revitalize these spaces.
The results could be tremendously positive. As Theresa Lynch, principal at Mass Economics says, “The people are already there. There are a thousand people with good ideas and they are looking for space.”
The spaces

Vacant Industrial Space in Cincinnati (Credit: Recast City)
Formerly vacant industrial buildings have proven very hospitable to small-scale manufacturing. Not all sites are created equal, though. In Detroit, pre-auto industrial buildings have proven to be the best for reuse. Former auto plants tend to be massive, and thus can be cost prohibitive to revamp and maintain. Pre-auto buildings have much smaller footprints, and are more affordable to get off the ground as spaces for small-scale manufacturing.
Pre-auto industrial spaces are also constructed remarkably well. “The ability of some of the older buildings to bear weight is amazing, relative to some of the newer spaces,” says Lynch. The structural systems are in fact over-engineered, far stronger than what is required by code. “They’re basically tanks,” says Kinkead, “so you can do a lot with them.”
Since these buildings were made for manufacturing, there is a higher capacity for water delivery, as well as relatively high voltage already being delivered. This comes in handy for manufacturers that needs to run power tools or heavy machinery, for example.
With all of these systems already in place, revitalization of the spaces for manufacturing just makes sense. Not only is it economically sensible, but it is also more sustainable by taking advantage of the existing built environment. “If you built these buildings today you would have a high capital cost, but through reuse you don’t accrue those costs, and you are not wasting things,” says Kinkead. “There is an inherent efficiency in this.”
A resilient network

Coworking Space at Ponyride (Credit: Chris & Michelle Gerard)
Many of these revitalized spaces follow an incubator model, gathering different enterprises under the same roof. A good example is Ponyride in Detroit, which houses everything from metalworking to coffee roasting to an enterprise that sews overcoats for the city’s homeless.
This shared-space model helps defray the start-up costs of launching a business, and also means that fledgling enterprises don’t have to deal with potentially difficult things like liability insurance.
Theresa Lynch calls this shared-space model “blue-collar innovation space.” Over the past decade, shared-space office models have exploded across the country, but they are mostly limited to people who work desk jobs. There is a whole section of the economy that requires more physical work that has been left largely out of the picture. Lynch remarks, “There’s this growing sense that some of the innovations in real estate have to grow beyond people that write software apps.” The reuse of vacant industrial space is key to supporting the development of these new blue-collar shared spaces.
Another one of the benefits of the shared-space model is that it can develop a real community of innovation. “I think the real value of these smaller scale facilities is establishing ecosystems and networks, sharing ideas and products,” says Kinkead. Working in community, start-ups can learn from one another and help each other to grow.

Small-scale manufacturer at work (Credit: Stitch & Rivet)
And this model is inherently more resilient than its large-scale industrial predecessors. “Cities with a diverse set of small businesses can weather market changes more successfully and are less likely to lose their growing businesses to other cities or countries,” says Ilana Preuss, founder of Recast City, a new organization that helps cities overcome hurdles to reusing industrial space. Preuss has seen developments like these find success all across the country, from Brooklyn to Indianapolis to Cincinnati.
“In the past, we had big enterprises,” said Kinkead, “and so when they went down or relocated, a lot of people would relocate with them,” leaving these large industrial buildings vacant in their wake. With this new model, some enterprises will succeed and some will fail, but none are at a scale where the closure causes wide-ranging economic devastation.
Regulation + Prioritization
In thinking about how to foster small-scale manufacturing, cities can also promote the combination of housing and industry in the same spaces. Detroit Future City has called for the creation of “live+make” spaces in order to reuse industrial spaces for a combination of residential use and small-scale manufacturing. In order to accommodate this model, however, Detroit will need to be intentional with its zoning policies.
“We think there should be policy and regulation that specifically calls small-scale manufacturing out,” said Kinkead, “Small-scale manufacturing is not currently contemplated in Detroit’s master plan and zoning and it should be.”
And regulation of these rehabbed spaces will only become more important as they become more prominent and successful. “Over time as these things grow, the growing legitimacy will draw greater scrutiny,” said Dan Kinkead. Hopefully cities will be able to find a way to regulate these spaces that preserves health and safety without discouraging the continued growth of small-scale manufacturing.
Cities should also be strategic about selecting the industrial corridors in which they focus on promoting small-scale manufacturing. “When you have multiple options, don’t try and do everything 10 percent,” says Lynch. “Think, where do we want things to be growing in 10-20 years?” By strategically looking at market and investment projections, cities will more successfully be able to support the growth of small-scale manufacturing.
Conclusion
The collapse of the manufacturing sector toppled the local economies of America’s Legacy Cities, causing widespread disinvestment and population loss and leaving a massive number of vacant and abandoned properties in its wake.
It may be manufacturing, however, that helps bring about the reactivation of these vacant spaces. Through smart public policy and private investment, manufacturing can again be a job creator in the very buildings it left behind vacant decades ago.
It will just look a little different this time, with smaller enterprises coming together to create an innovative ecosystem, producing the local goods that people want.
Subscribe to join 14,000 community development leaders getting the latest resources from top experts on vacant property revitalization.